5 Great Reasons to Choose Foil Tape
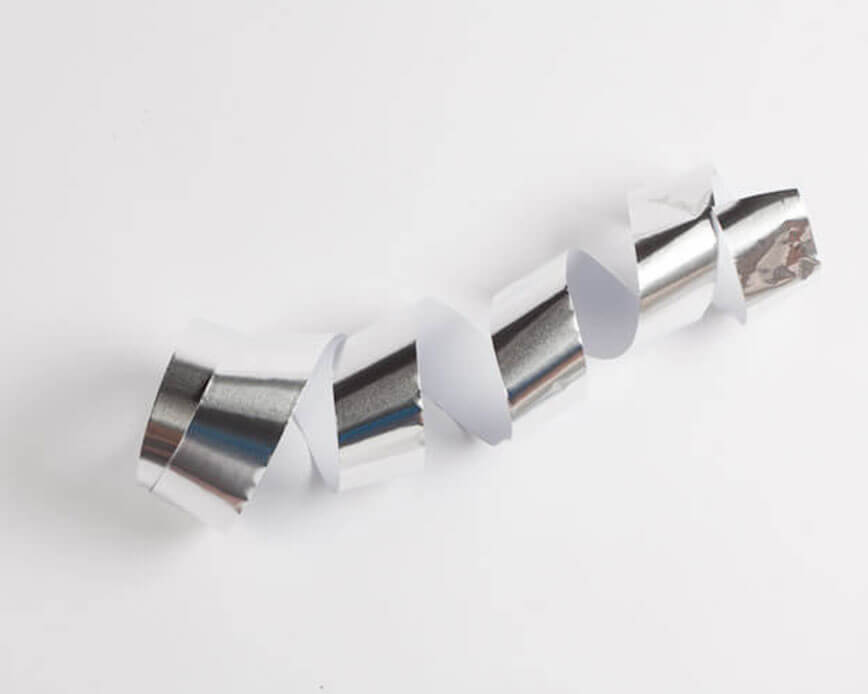
Combine the versatility of aluminum and the weather-resistant sealing power of adhesive tape, and you have an extremely versatile product — aluminum foil tape.
Foil tape is so versatile that it is widely used in all kinds of industries, from manufacturing to construction.
Thanks to its moisture and chemical resistance, thermal conductivity, flame resistance, heat and light reflectance, and weatherability… it makes for a tape that has a wide range of applications.
What is Foil Tape, Exactly?
Aluminum foil was first available in 1888, and commercial production in the U.S. started in 1913. Prized for its protective qualities and attractive appearance in containers and packaging, it was widely used in World War II to protect packages, electrical capacitors, and insulation. After the war, it became available for commercial use.
Foil tapes use a specially-engineered metal-foil backing which contributes to the tape’s malleable, conductive, and rugged characteristics. Foil tape carriers include aluminum, aluminum with glass, lead, copper, copper with tin plating, and steel.
That said, when it comes to building and construction, aluminum foil tape is the most widely used foil tape. All told, here at ECHOtape, we engineered our foil tapes to have all the qualities of aluminum with the added benefit of an aggressive and long-lasting adhesive.
Why Choose ECHOtape Aluminum Foil Tape?
Here are the top five reasons why our foil tape has become a best seller with so many of our customers:
1. UL 723 rated and meets International Building Code standards.
UL 723 is a test to measure the surface burning properties of building materials. In particular, it looks at the rate of flame spread and the density of smoke developed. To meet the International Building Code’s definition of fire-resistant, a composite material must have a flame spread rating no higher than 50.
ECHOTape’s foil tapes are UL723 certified, which is worth noting because not all cloth-backed duct tapes or foil tapes are UL 723 rated.
2. Extreme cold and heat temperature versatility.
Our foil tape works in temperatures ranging from 248°F to -22°F and can be applied in temperatures ranging from 14°F to 104°F. Most tapes do not perform well in cold temperatures. Severe cold hardens the adhesive and diminishes sticking power of the tape. If you are applying the tape under cold conditions, it may not stick at all. Conversely, excessive heat can melt the adhesive on some tapes, rendering it useless.
3. Made with an acrylic adhesive.
ECHOtape’s all-weather aluminum foil tape is coated with a superior performance flame-retardant solvent acrylic adhesive, working equally well in extreme hot and cold weather conditions.
Why does this matter?
Well, most duct tapes are made with a rubber adhesive, which is known to delaminate from its backing in high-temperature applications. Other synthetic rubber adhesives may offer a greater range of temperature functionality, but they also have lower mechanical strength, weak aging resistance, and do not fare well under UV light. By creating a foil tape with an acrylic adhesive, we’ve achieved superior durability and longevity once they cure and stick to a surface.
4. A great alternative to mastic.
Our aluminum foil tape products are not messy (the biggest drawback of mastic), and they use less equipment (no need for old clothes, eye protection, gloves, paint brushes, drop cloths, etc.) It doesn’t need additional fasteners such as sheet metal screws, scrap metal, and drywall mesh to seal large areas and it can be used to seal holes in a furnace or air handler.
5. Able to hold up over time.
In construction, pressure-sensitive tapes are often used in areas that are concealed (like housewraps or foil-faced insulation). Which means they cannot be easily repaired or replaced. Due to its acrylic adhesive technology, aluminum foil tape offers better cohesion, adhesion, and thermal stability than a tape with a rubber adhesive.
To put it another way, ECHOtape’s line of foil tape products are designed to hold up to temperature fluctuations, exposure to UV light and other solvents that would typically impact and breakdown the adhesive effectiveness of different types of tape, making them the ideal choice for both construction and industrial applications.
How to Insulate and Seal HVAC Ducts: An Example of a Foil Tape Application
According to the U.S. Environmental Protection Agency, “In typical houses, about 20% of the air that moves through the duct system is lost due to leaks, holes, and poorly connected ducts. The result is higher utility bills and difficulty keeping the house comfortable, no matter how the thermostat is set.”
Like a leaky faucet that slowly and steadily wastes water, your HVAC system’s ducts can prove a sure place to lose dollars, waste energy, and sacrifice air quality. Insulating ducts with insulation can help with this issue, and ensuring the insulation is sealed well is the place to use foil tape.
Follow these steps to insulate and seal ducts with aluminum foil tape:
- Inspect all the ducts for holes and to ensure seams between the ducts and joints are tight. Seal any leaks/breaches with foil tape.
- Consult with the insulation manufacturer’s instruction on how to measure the length of insulation required so it will encircle each duct well and neither be too tight so it compresses the duct nor too loose so it is ineffective.
- For an excellent fit, you can trim away about 2 inches of the insulation from the backing to fashion a flap that can overlap the end of the wrapped piece and provide a smooth surface on which to place the tape.
- Wrap the insulation around each duct, allowing the vapor barrier backing to face out.
- Carefully seal every seam with the foil tape.
- Continue along the length of each duct, ensuring that every roll of insulation is securely taped to the adjacent strip of insulation.
- Besides cost savings and system efficiency, air quality is improved when an HVAC system works as designed. A home’s duct system, once compromised, can serve as a transport method to disperse particles like dust which can easily exacerbate respiratory and allergy conditions.
Furthermore, we believe it’s a good idea to inspect your ductwork periodically, especially in the following scenarios:
- After an installer or repair person has worked in your attic. A simple misstep can cause duct damage. Even an accidentally dropped tool may create a small hole that can add up to significant energy loss. (A foil tape patch will save the day!)
- If you are upgrading your air conditioning system and don’t wish to spend the money to have the ductwork replaced, an inspection and a little foil tape can go a long way to more reliable ductwork for an optimally functioning and energy-efficient system. The most highly rated HVAC units are nothing without adequately sealed ducts.
- If you are seeing an unsubstantiated rise (one not the result of a provider’s cost increase) in your utility bills
- If specific spaces or rooms seem difficult to heat or cool
Sealing and insulating your ductwork will go a long way to an economical, better climate controlled, and cleaner environment.
At ECHOtape, we offer a full range of specialty tapes that can work in all kinds of circumstances, like the aluminum foil tape solutions listed above.
To learn more about adhesive tape, refer to our Technical Guide to Adhesive Tape. Or, contact the ECHOtape team with your tape request if you want help determining which product is best for your particular project.
Click here for our complete selection of insulation tapes.
Also, check out some of our most popular tapes:
Outdoor double sided tape
Thermal tape
FSK tape